One of the factors that enhances comfort within a building is its airtightness, which also helps reduce energy use. Through the Blower Door test, we detect air infiltrations so that we can act to eliminate them.
The airtightness of a building's envelope directly influences the energy consumption of the building. The more airtight the building, the less it consumes. This value is theoretically taken into account in the energy certification, but is rarely checked once the building is completed. In this article we will look at what airtightness is and how it differs from thermal insulation, how it contributes to energy savings, the principles and materials for airtight construction, as well as common mistakes to avoid.
What is airtightness and what are its benefits?
Airtightness comes from the word airtight, i.e. it closes tightly so that no air can get through. The airtightness is the "skin of the house" and must control the watertightness, preventing the uncontrolled passage of air into the interior. This concept should not be confused with thermal insulation, which is the ability of materials to oppose the passage of heat by conduction. Both properties are important for the building envelope, but they must be achieved independently.
Achieving a good level of airtightness inside a building offers multiple advantages; among others:
- Prevents the ingress of harmful gases or particles.
- Avoid draughts.
- It prevents water ingress and, therefore, pathologies caused by dampness.
- Improved protection against noise (both airborne and vibration in the building structure).
- Improves energy efficiency.
What tests are performed to verify it? Blower Door tests in residential buildings
The blower Door test is a test that measures the airtightness of a building and detects air infiltration. This airtightness or watertightness test, which is carried out in accordance with the European standard UNE-EN ISO 9972:2019, is aimed at determining the level of permeability of the building envelope by pressurising or depressurising it. A fan is usually installed at the front door or access door of the house and measures the pressure difference of 50 Pascals between inside and outside. The results obtained correspond to the total air volume renewals per hour.
In some European countries, its use is common and is required in new construction as an overall test of the quality of construction finishes. In Spain, although it is increasingly used as a test of the quality of the envelope in new buildings and to detect construction defects in existing buildings, it was not until the arrival of the CTE 2019 that the requirement for air permeability of the thermal envelope of the building as a whole was incorporated.
However, the Blower Door test —which is the only way to check this permeability— is not compulsory in Spain as long as you comply in a prescriptive way (i.e. by calculation) with the requirements defined in section HE1 of the CTE. These requirements must comply with 3 to 6 ren/h depending on the compactness of the building by means of a formula; if not, it must be demonstrated by means of a Blower Door test. This only applies to new buildings in private residential use with a total usable floor area of more than 120m2.
What results do we usually encounter? Normally, we observe that the values we measure when performing Blower Door tests are far from the theoretical results. In the test of this type that we usually carry out in multifamily residential buildings, the values obtained are usually above the recommended limits for a standard dwelling or construction, which should not exceed 6 air changes per hour at 50 Pa.
When the values are above the expected values —only one in six dwellings is within the recommended limits— the dwellings are inspected for leakage. For this we use the thermographic camera and the smoke machine and a visual inspection of the hidden areas: false ceilings, passages of facilities, connections to adjacent dwellings, etc.
The most common pathologies we detect are the non-motorized shutter boxes (entries through the belts and boxes) as one of the main pathologies, along with air entries through:
- The joint between the facade and the frame, between the sash and the frame, and the closing plate of the windows.
- The mechanisms mounted on the kitchen facilities drawer.
- The main electrical panel.
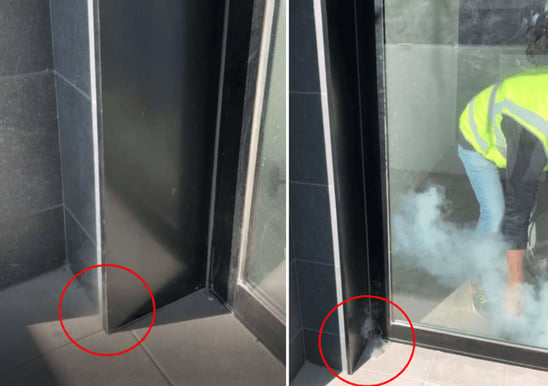
Keys to ensuring watertightness: sensitive areas and materials
How can we work to improve the results? The work process must be comprehensive, from the basic project to the end of the work.
- Definition of construction solutions in the design phase.
- Training of the DE, DO, technicians, and installers.
- Choose a representative space of the project (Pilot Space) where airtightness measures are developed, implemented, and tested. Some of the actions to be developed in this phase are:
- Hold a meeting to put all the agents involved in the execution of the envelope in contact: Execution Management, the Construction Company, and all the technicians and installers involved.
- Review all the shutter boxes.
- Place rubber seals on the handles of the sliding windows.
- Validate the sealing materials to be used.
- Perform a specific test on a window once installed to determine if it meets the airtightness class indicated by the manufacturer.
- Perform an inspection of the sealing of vertical and horizontal facilities passages, and junctions between slab-facade and slab-interior partition prior to the installation of false ceilings.
- Seal the air vents through the frame, covering the corrugated tubes for electrical and telecommunications connections to the homes
- Blower-door tests in the pilot space until achieving the target result.
- Replicate the measures defined in the pilot space to the rest of the spaces in the building.
- Periodic work monitoring.
- Final Blower-door.
The problems of lack of airtightness due to poor execution are usually due to errors made during the building execution phase. There are certain sensitive areas in the envelope where this property must be taken care of to eliminate thermal bridges and achieve an optimal level of watertightness; these are mainly:
Openings and structural connections
The CTE 2019 (DB-HE1) talks about "taking care of the joints between openings and opacities". Air seeps through the gaps in the joints or perimeter trims of exterior doors and windows, as well as through the joints between building elements such as facades, floor slabs and envelopes, impairing their energy efficiency.
Also, shutter boxes and lift doors are critical areas for air ingress into the house. These elements require special care when sealing between materials to ensure the continuity of the thermal envelope.
Misaligned shutter boxes
Pipes, cables, and facilities boxes
The ducts that pass through the thermal envelope: facilities passages through the envelope and ventilation, flue and drainage ducts. We must ensure that they are well sealed to avoid indoor air drafts and thus guarantee the airtightness of the building.
Lack of sealing of facilities
Electrical boxes, cable ducts (vertical conduits with cables and pipes through the different floors of the building) and spaces that house installations must also be insulated to ensure airtightness.
What products to use?
In the market, we can find different products that improve the airtightness in these sensitive areas. Products that are typically used in energy efficient buildings such as passive houses, under the Passivhaus standard, and near-zero energy buildings. Some of these solutions include:
- Expanding foam tapes: they provide a resistant seal with a high degree of leak-tightness both to air — preventing ingress through joints and intersections between the envelope and the doors and windows on the facade — and to water. Additionally, they reduce the entry of external noise.
- Elastic and controlled expansion foams: they are applied using a gun and create airtight barriers on the surfaces of the thermal envelope, providing a high level of leak-tightness.
- Liquid waterproofing membranes: once dried, these polymer pastes applied with a brush or spray machine form flexible membranes that improve the airtightness in sealing the connections between construction elements.
It is necessary to work from the design phase with proposals for specific construction details that propose solutions to improve airtightness. These solutions, moreover, must be evaluated to avoid additional costs when applying them in the project. It is also necessary to train site technicians to apply them and to supervise their correct application. If this part is executed correctly, it is certain that a good result will be obtained when the blower door is tested afterwards.